精益与看板学习笔记
- 2018-03-07 10:10:00
- 红哥谈测试
- 转贴:
- csdn
- 1174
精益与看板学习笔记
关键词:
精益、内建质量、 TPS 、《丰田之道》( 2001 )、 TPS 、看板
精益的起源
西方制造业:通过规模化生产,降低成本、提高生产效率和质量
丰田制造:通过精益化生产,更加降低成本、更加提高生产效率和质量,而且响应速度更快。
精益的目标是消除浪费,以更多的交付有用的价值。
精益的 2 个支柱和 5 个价值观
一、持续改进
1 、挑战现状
2 、改进,持续改进,不断追求创新和进化
3 、现地现物,从源头发现事实,做出正确决策,建立共识,快速达成目标
二、尊重
4 、尊重他人,理解对方,承担责任,建立互信
5 、团队协作
精益产品开发的原则
原则 1 、探索和发现有用价值。做正确的事,是业务成功的根本。
原则 2 、聚焦和提升价值流动效率
精益的 5 个实施步骤(精益的方法)
1 、定义价值,从用户的角度定义,并描述为产品或服务
2 、识别价值流,识别和映射创造价值的流程步骤,消除不增加用户价值的步骤和活动
3 、让价值持续流动,让用户价值在流程步骤中持续、顺畅的流向用户
4 、用户价值拉动,由用户价值拉到流动,避免浪费
5 、精益求精,重复 1-4 ,不断完善
精益实践
1 、准时化( Just In Time , JIT ),即时生产,需要的时候才生产(降低库存)
2 、自动化,出现问题时,生产过程自动停止,迫使现时现地解决问题(质量内建于每个环节)
3 、看板,通过最下游的客户价值(需求),拉动上游的生产环节。
看板,“信号卡”,最早出现在丰田生产系统( TPS )中。
看板系统是一种“通过向上传递信息流,拉动向下物流”形成的拉动式生产系统。
拉式生产与推式生产的效果比较,可用回形针构成的链条形象比喻:
1 、控制库存,下游需要时,上游才生产。
2 、加速流动,保证安全库存的前提下,物料最快的流动。
3 、灵活响应,用户的需求变化,通过看板形成的信息流,快速传递到上游各环节,系统做出最快响应。
4 、促进改善,生产环节的问题可第一时间暴露,为尽快解决提供了便利。
最终让用户价值顺畅、高质量的流动。
看板的核心实践
一、建立看板系统
1 、可视化价值流,包括:
( 1 )让用户价值可视化,如可验证、可交付的需求
( 2 )让用户价值端到端的流动过程可视化
( 3 )让问题和瓶颈可视化
2 、显式化流程规则,明确价值流转的规则,包括:
( 1 )工作项状态转移的标准(从一个环节进入下一环节)
( 2 )其他协作规则(活动节奏、组织方式、优先级、问题处理机制等)
3 、控制在制品数量
n 限制在制品数量,事实上形成了一个拉动机制,下游顺畅时,才能从上游拉入新的工作,最终拉动整个价值流动的是用户价值的交付。
n 控制在制品数量是看板方法的核心,也是最容易引起争议的地方,如实施过于困难。
二、运作看板系统,让用户价值在看板系统中顺畅、高质量的流动
4 、管理工作的流程,管理价值的输入、中间过程、输出,对应于:
( 1 )就绪队列填充会议(待办项列表建立会议)
( 2 )每日站立会议
( 3 )发布计划会议
5 、建立反馈并持续改进
( 1 )流动是否顺畅的反馈
( 2 )质量问题的反馈
联系人: | 阿道 |
---|---|
电话: | 17762006160 |
地址: | 青岛市黄岛区长江西路118号青铁广场18楼 |
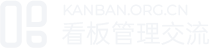
专注看板管理学习交流