JIT看板管理
- 2021-02-11 10:00:00
- liuous
- 转贴:
- IT PUB
- 1328
准时化:将需要的零件,在需要的时间,按照需要的数量供给每一道工序。
上世纪70年代时任丰田汽车工业副社长的大野耐一提出了丰田式生产方式,他认为:推式绝对无法很好的完成准时化。但是要知道:改变成拉式的思路仅仅是思考的方法,实际的生产作业还是由上序流向下序。二者真正不同的地方只是在于信息传递的方向和时机。
自働化:使机器能够判断产品状态好坏的装置。
自働化为一个人能操作多个机台提供了有效的支持,其作用描述成防错装置比较合适。但要注意的是:防错装置的产生来源于产生过的或者类似的错误。在这点上TPS和FEMA(失败模式和影响分析)有相通之处,他们最大的特点是能及时发现并处理问题。
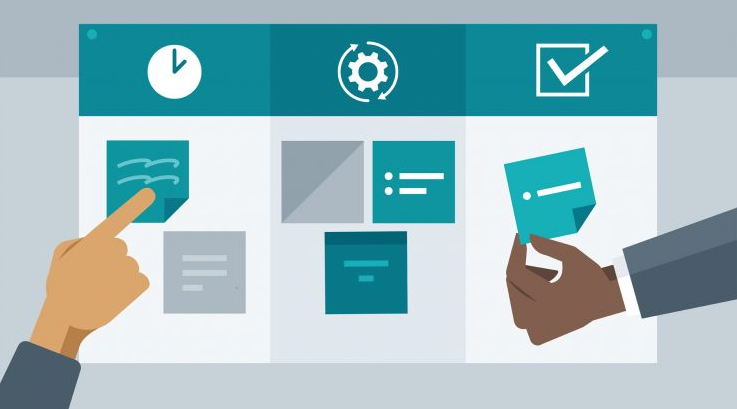
而要想做到准时化生产,以下三点非常关键:
- 均衡化生产(标准化生产);
- 改善——消除浪费;
- 看板。
准时化生产是针对流水线作业类型的生产方式来说的,因为相对来说,流水线的生产方式具有更短的交付期,在工序多的时候更加具有优势,为准时化生产提供了基本的保证。而TPS追求的极致,就是一个流。如果要准时化生产,就要求所有的零件加工以同一个速度流动;如果要按照生产节拍布置,生产线就成为必须,所以必须进行U型布局。
而我们知道:流动的速度决定于需求。那么生产节拍=可用工作时间/客户需求数量。例如:每周工作5天,每天工作8小时,顾客的需求量是800,那么生产节拍=5*8*60/800=3分钟。
需要注意的是:丰田公司通常每月评审一次生产节拍,每10天进行一次调整检查。那么什么是滚动计划呢,以丰田为例:
- 丰田公司接受的销售预测是三个月,制造部门用销售预测来制定基本生产计划(相当于普通生产方式的MPS)和调整生产节拍;
- 销售部门把每天接受的信息汇总后,每旬也会调整一次,制造部门用这个旬计划来制定整车交付的顺序计划表;
- 每日的更新也会及时通过销售传递到制造部门。
这样,更新的信息源源不断的输入制造工厂,丰田制造工厂在整车下线前四天还可以调整整车的最终规格。
从这里我们可以看出:滚动计划相当于一个水库;输入和输出不断更新反馈,通过总容量均衡的调节,避免波峰波谷的出现。
一、追求均衡的代价如何挽回?
均衡生产是尽量把不同的品种在生产线上予以平均化,避免生产的时候一个品种产生波峰波谷。诚然,品种均衡会导致生产效率的下降,但是相对于顾客随机的必须满足的需求和避免主机厂和供应商存货损失来看,这点机会成本确实是微不足道。
以丰田的实际生产为例:客户需求量是每月10000辆花冠,轿车5000辆,硬盖车2500辆,旅行车2500辆,每月工作20天。生产线流动方式是每隔1台是轿车,每隔3台是硬盖车和旅行车。如下面所示:ABACABACABACABAC。从这样的方式可以看出: 丰田追求的也不是绝对的均衡,而是有限度的。追求均衡是有代价的,因为频繁更换产品有肯定能造成生产的前置准备时间加长,丧失了批量生产的效率。
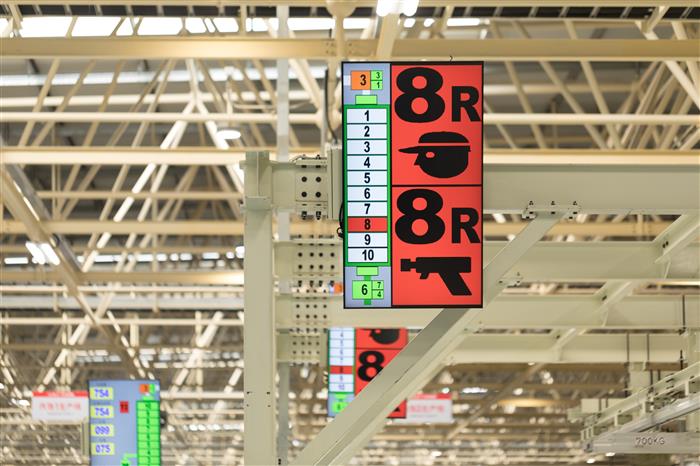
同时,支持均衡生产的另外一个支柱就是FMS(Flexible Manufacturing System),也是缩短前置时间的保证措施。FMS就是通过微机中记忆的生产计划程序,起着自动控制变更各种规格、加工时间、批量规模等作用。
引入JIT需要一份标准作业表当老板们喊着要引入JIT的时候,应该到现场看看,工人是否按照作业指导书操作。而且基于IE的标准作业表就是大野耐一坚持现场管理人员亲自编制的——丰田的工艺人员必须亲自操作之后,才能通过审核。
丰田公司的标准作业表上记载着 标准作业的三个要素:
- 周期时间;
- 作业顺序;
- 标准手持(标准存活量)。
浪费有如下七个表现:
- 过量生产的无效劳动;
- 窝工的时间浪费;
- 搬运的无效劳动;
- 加工本身的无效劳动和浪费;
- 库存的浪费;
- 动作上的无效劳动;
- 制造次品的无效劳动和浪费。
或许大家把以上的浪费的种类进行重要性排序,可能会得到很有趣的结论。因为以上的浪费很难用量化的数字来表示,但是排序的结果的确反映了我们的管理心态,并且给我们的管理改善指出了方向。
在丰田是通过什么方式消除浪费的呢?如何做到如此有效的呢?那就是以降低成本为目标的全员参与的改善活动,而且已经形成了良好习惯的合理化建议。因为在丰田的观念中: 没有人比操作者更清楚浪费在哪里产生。
二、看板的作用是什么?
看板是顺利推行丰田生产方式的手段。从看板的作用来看,看板不是生产计划,而是具体的操作指令信息。看板分为生产看板(Production Kanban)、一般生产看板、三角看板(批量生产看板)、取货看板(Withdrawal Kanban)、厂内(工序间)取货看板、外协厂取货看板等。
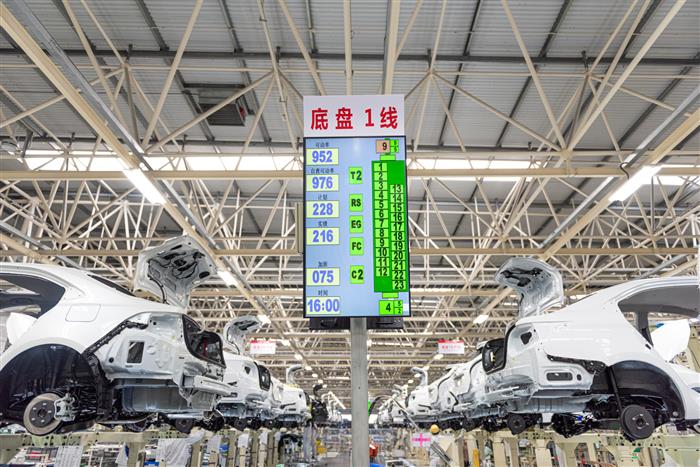
前面提到的 自働化在企业中是如何运用的呢?这里举例说明:
- 工序N加工零件AL,AL和AR左右对称,很容易混淆,那么在零件上增加一个的定位孔,夹具上增加一个定位销,使AR在工序N无法进行加工。
- 工序N加工零件B,如果漏了一个钻孔工序,下序无法装配,那么在周转箱内增加一个凸点,漏了钻孔,零件就无法摆放。
- 工序N进行焊接,如果电流不够,自然无法保证焊接强度,增加一个电流反馈,无法达到工艺参数,报警。
- 流水线某工位发生质量问题,工人有权利启动停止开关。
人为的因素很多:不熟练、疲惫、心情都可能影响产品的质量。那么针对这些就有一个补救的 自働化的方法来消除,比如FEMA。
至于设备,就涉及到TPM(Total Productive Maintenance)的管理方式。最重要的一个指标就是设备综合利用率,最重要的方式就是类似FEMA的分析方式:用日常点检的方式保证设备正常运转,用标准故障的分析和排除保证最短时间修复设备。
联系人: | 阿道 |
---|---|
电话: | 17762006160 |
地址: | 青岛市黄岛区长江西路118号青铁广场18楼 |
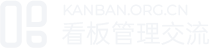
专注看板管理学习交流